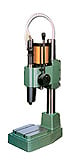
Durable Technologies' pneumatic impact presses are simple to set up, easy to operate, and offer excellent repeatability. They provide significant advantages in terms of control, safety, and reliability, and are low maintenance.
Pneumatic presses are best suited for higher-volume marking requirements. Your pneumatic press can be operated automatically using hand controls or manually by pulling the lever.
In addition to stamping and marking, our presses can be used for many other manufacturing applications including: riveting, staking, forming, punching, bending, notching, crimping, piercing, assembling, broaching, and coining.
Durable Technologies' impact presses can be supplied as a turnkey package including custom steel stamps, steel type, type holders, and manual or automatic numbering heads depending on your specific part marking requirements.
We can also help you design a custom fixture for your parts to ensure operator safety and a consistent mark every time.
Check out this blog post that covers the versatility of our impact presses across a variety of manufacturing applications.
Read this application story from one of our customers.
Pneumatic Impact Press Principles of Operation:
Since these presses operate on a spring-actuation principle, the degree of impact is easily adjustable. The press contains a spring that is compressed during energy section travel.
Press capacity can be easily adjusted by increasing or decreasing spring size and/or tension. When the release point is reached, the compressed energy is discharged causing the internal hammer to deliver a powerful impact.
There are a variety of sizes of springs available for each of our impact press models. Vertical travel is accomplished by a gear and rack arrangement.
Step 1 - The energy section advances towards the workpiece by gear rack and pinion, powered either automatically by a double-acting pneumatic cylinder (if using a pneumatic unit with hand controls) or manually by the operator pulling down the lever.
Step 2 - Once the press stroke is engaged and the workpiece is contacted, the press stroke continues. The workpiece is held in place by the pressure from the energy section (this is a significant safety feature.) The impact spring is compressed and builds force as the press continues to maintain contact with the workpiece.
Step 3 - When the ball bearings reach their release point, the powerful impact is discharged. The impact spring delivers force to the hammer, which in turn strikes the plunger (tool holder.) You can control the amount of impact depending on which spring you choose and how much tension is applied.
The impact presses' ease of operation, safety, consistency, and versatility make them a very popular solution for a variety of applications.
In addition to stamping and marking, our presses can be used for many other manufacturing applications including:
- Marking
- Stamping
- Riveting
- Staking
- Forming
- Punching
- Bending
- Crimping
- Piercing
- Assembling
- Broaching
- Coining
Our customers recognize the value of Durable Technologies' impact presses and realize benefits like:
- Simple to setup
- Easy to operate
- Excellent repeatability
- Consistent impact
- Impact adjustable by increasing impact spring tension
- Safety - the workpiece is held in place by the press during impact
Our engineers will work with you to provide custom fixtures and nesting for the most challenging shop press applications.
In addition to our Durable Technologies' line of impact presses, we also supply replacement parts for many of Automator's impact presses.
Contact us today and our experts will help you find the best tools to make your mark!