4 min read
Why Quality Coding Type Makes All the Difference
Matt Martin
Tue, Jul 08, 2025 @ 08:07 AM
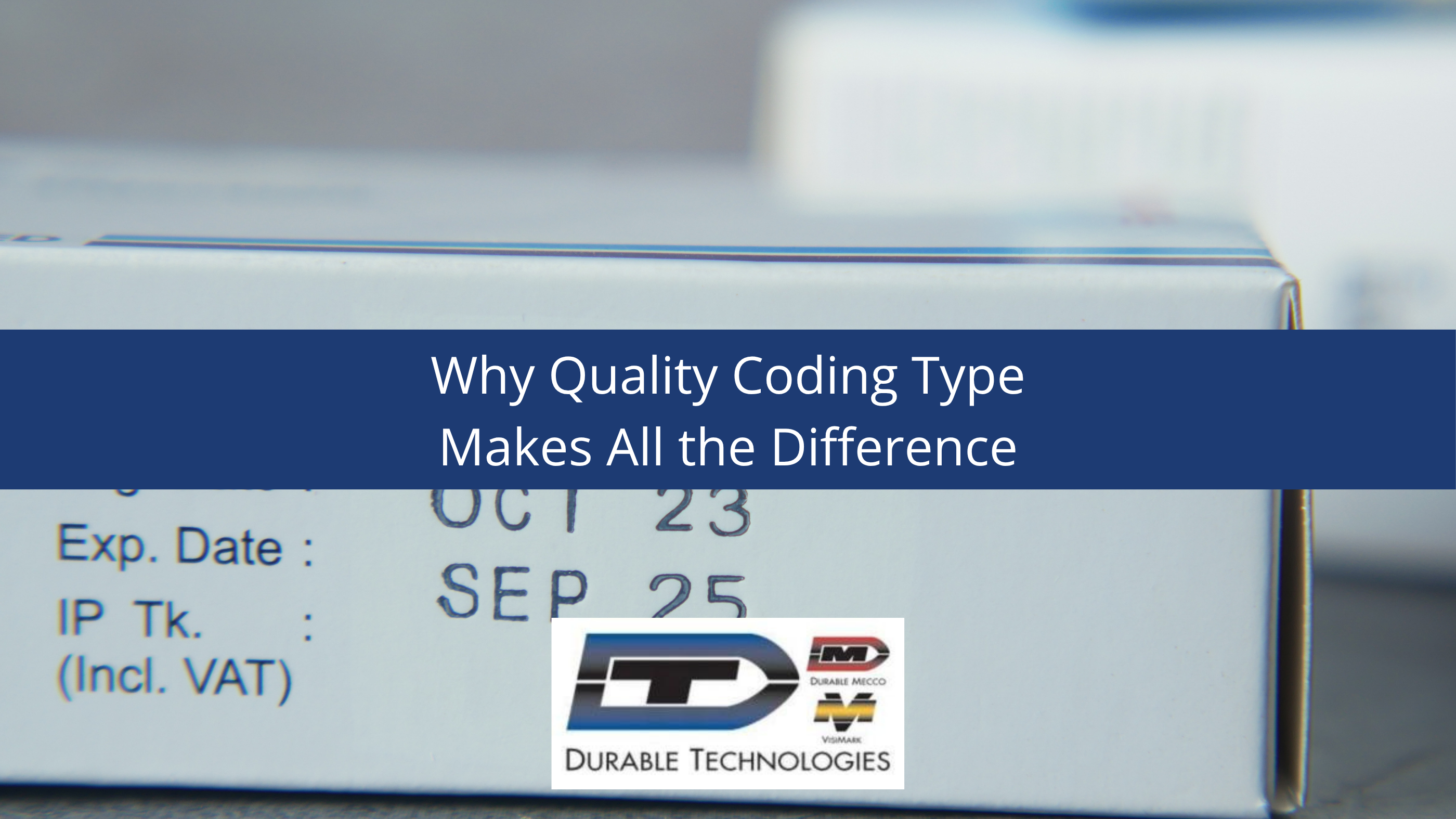
Picture this: you're standing in a grocery store aisle, reaching for a carton of milk. Without thinking twice, you check the expiration date stamped clearly on the side. That simple act—one we perform countless times each day—relies on a small but crucial piece of industrial technology that most people never consider: metal coding type.
Behind almost every crisp date code, every batch number, and every product identifier lies precision-engineered brass or steel dies that transform blank packaging into traceable, compliant products. While these tiny workhorses operate behind the scenes, their impact on product safety, regulatory compliance, and brand integrity cannot be overstated.
The Foundation of Modern Manufacturing
Metal coding type serves as the backbone of industrial marking across virtually every sector imaginable. From pharmaceutical companies ensuring medication safety through precise lot tracking to food manufacturers meeting FDA labeling requirements, these dies create the permanent marks that keep our supply chains transparent and accountable.
The beauty of quality metal type lies in its versatility. Whether you're embossing serial numbers into automotive parts, debossing company logos onto luxury packaging, or imprinting expiration dates on food containers, the right die can handle materials ranging from delicate foils to robust corrugated cardboard. This adaptability explains why major OEM equipment manufacturers have built their coding systems around interchangeable metal type for decades.
When OEM Parts Fall Short
Here's where things get interesting for manufacturers. While original equipment manufacturers produce reliable coding systems, their replacement parts often come with significant drawbacks that impact both operational efficiency and bottom-line performance.
Long lead times frequently disrupt production schedules, sometimes forcing manufacturers to halt operations while waiting for critical components. The financial sting becomes even sharper when you consider OEM pricing structures, which typically include substantial markups that reflect brand premiums rather than manufacturing costs.
Quality concerns present another challenge. OEM parts aren't always manufactured to the exacting standards that demanding industrial applications require. When your production line relies on consistent, clear marking day after day, subpar dies can lead to costly quality control issues, rejected batches, and regulatory headaches.
The Alternative That Works
Smart manufacturers have discovered that OEM-alternative suppliers can deliver superior value without compromising quality. The key lies in finding a partner who understands both the technical requirements of precision die manufacturing and the operational realities of modern production environments.
Take the complexity of equipment compatibility, for instance. Today's manufacturing facilities often run a diverse mix of coding equipment—perhaps Norwood imprinters for flexible packaging, Markem touch dry coders for pharmaceutical applications, and Jones cartoners for consumer goods. Rather than managing multiple supplier relationships with varying quality standards and delivery schedules, working with a comprehensive alternative supplier streamlines procurement while ensuring consistent performance across all equipment types.
The manufacturing precision required for quality metal coding type demands sophisticated metallurgical knowledge and machining capabilities. Brass dies need specific alloy compositions to resist wear while maintaining sharp impressions. Steel dies require careful heat treatment to achieve the hardness necessary for marking tough substrates without premature failure. These aren't generic metal parts—they're precision instruments that must perform reliably under demanding conditions.
Beyond Cost Savings
While the financial advantages of choosing OEM alternatives are compelling—often delivering 30-50% cost savings compared to original parts—the operational benefits frequently prove even more valuable. Shorter lead times mean production managers can maintain leaner inventory levels without risking costly downtime. When a die wears out unexpectedly, getting replacement parts in days rather than weeks can save thousands in lost production.
Customization capabilities represent another significant advantage. OEM suppliers typically offer limited options, forcing manufacturers to adapt their processes to available parts. Alternative suppliers with in-house manufacturing capabilities can create custom dies tailored to specific applications, whether that means unusual character sizes, special alloys for harsh environments, or unique mounting configurations for modified equipment.
The Quality Question
Skeptical manufacturers often worry about quality when considering alternatives to OEM parts. This concern is well-founded—after all, coding failures can lead to product recalls, regulatory violations, and a damaged brand reputation.
However, quality alternative suppliers often exceed OEM specifications precisely because they must earn customer loyalty through superior performance rather than relying on captive market dynamics.
The best alternative suppliers invest heavily in quality control systems, advanced manufacturing equipment, and metallurgical expertise. They understand that their success depends on proving themselves superior to established OEM suppliers, not merely competitive. This dynamic creates powerful incentives for innovation and quality improvement, benefiting end users.
Looking Forward
The industrial marking landscape continues evolving as manufacturers face increasing pressure for traceability, sustainability, and cost efficiency. New regulations require more detailed product coding, while environmental concerns drive demand for longer-lasting dies that reduce waste. Simultaneously, global supply chain disruptions have underscored the risks associated with relying on single-source suppliers for critical components.
These trends favor alternative suppliers who can adapt quickly to changing requirements while maintaining reliable supply chains. Their flexibility in manufacturing custom solutions, combined with shorter supply chains and more responsive customer service, positions them well for an uncertain future.
For manufacturers still relying exclusively on OEM replacement parts, the question isn't whether alternatives can match OEM quality—it's whether they can afford to ignore the operational and financial advantages that quality alternative suppliers provide. In today's competitive environment, every efficiency gain matters, and the hidden heroes of product identification deserve suppliers who match their reliability and precision.
The next time you check that expiration date or scan that serial number, remember the precision engineering that makes it possible. Behind every clear, durable mark lies a carefully crafted piece of metal that represents decades of metallurgical knowledge, manufacturing expertise, and relentless attention to detail. Whether that die came from an OEM or a quality alternative supplier might not matter to consumers—but it certainly matters to the manufacturers who depend on consistent, reliable marking to keep their operations running smoothly.
About Durable Technologies
As the premier OEM-alternative type supplier in the country, Durable Technologies manufactures brass and steel dies and packaging type used for coding, imprinting, labeling, embossing, and debossing.
We are the largest manufacturer of replacement metal coding type for all of the popular OEM equipment, including Norwood® Imprinters, Markem® Touch Dry Coders, Jones® Cartoners, Open Date® Labelers, Norden® Tube Fillers, and many more.