3 min read
Pneumatic Impact Presses vs Manual Hand Stamps for Part Marking
Matt Martin
Tue, Jul 22, 2025 @ 08:07 AM
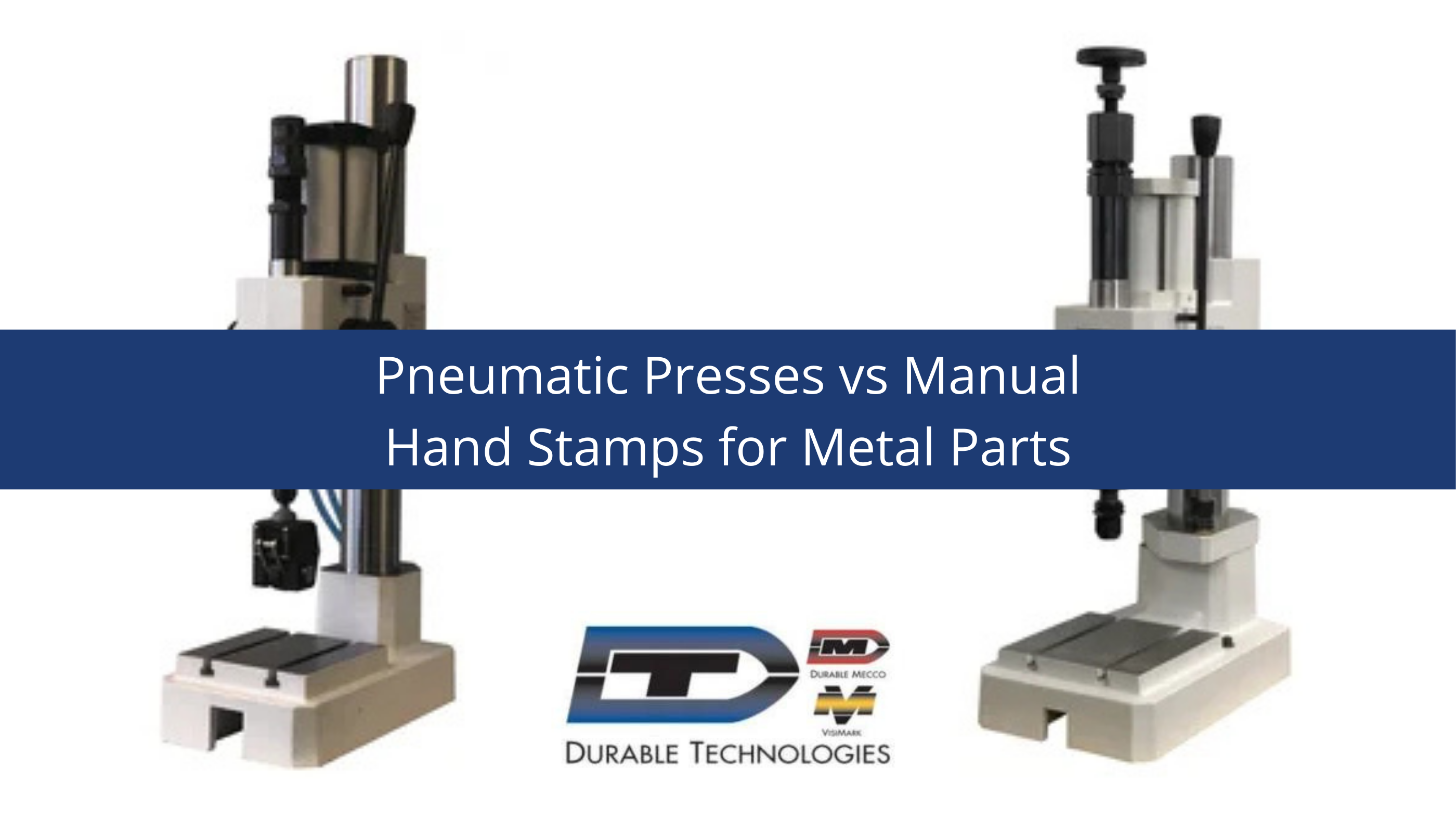
Production managers at small to medium-sized manufacturing companies are constantly having to weigh cost against efficiency, quality against budget constraints. When it comes to marking metal parts, the choice between pneumatic impact presses and manual hand stamps often becomes a pivotal decision that can impact your entire production line.
Having worked with many manufacturers facing this exact dilemma, we've seen how the correct marking method can transform a bottleneck into a streamlined process—and how the wrong choice can create headaches that ripple through your entire operation.
The Manual Hand Stamp Reality
Manual hand stamping remains the backbone of many smaller manufacturing operations, and for good reason. The simplicity is appealing: grab your stamp and a hammer, position the stamp carefully over the part, and deliver one clean strike.
The cost-effectiveness of hand stamps makes them particularly attractive for startups and smaller operations. You're looking at minimal upfront investment—just the stamps themselves, a quality hammer, and ideally a stamp holder for safety. This approach works exceptionally well for low-volume runs where flexibility trumps speed.
However, the reality check comes when your marking requirement dictates that you have to stamp either larger characters or more characters at a time. The amount of striking force required increases dramatically when marking multiple characters at one time. What works for a single character becomes exponentially more challenging when you're trying to mark a complete part number or logo in one strike. Your operators fatigue faster, consistency becomes an issue, and production bottlenecks begin to emerge.
The Pneumatic Press Advantage
Pneumatic impact presses enter the conversation when your production volume starts pushing the limits of manual methods. These systems deliver consistent pressure every time, eliminating the human variability that can plague hand stamping operations. The operator simply positions the part into a fixture, activates the press, and gets uniform results regardless of their experience level or how many hours they've been working on shift.
The speed advantage becomes even more pronounced in medium to high-volume applications. While a hand stamp requires careful positioning, rocking to ensure flat contact, and precise hammer technique, a pneumatic press can cycle through parts with mechanical precision. This consistency translates directly to quality improvements—no more double impressions from hammer bounce or mishits, no more uneven marks from inconsistent pressure.
For operations marking harder materials like stainless steel, pneumatic presses prove their worth. Where hand stamping stainless requires heavier hammers and more force (increasing operator fatigue and potential safety concerns), pneumatic impact systems deliver the necessary pressure without breaking a sweat.
The Safety Factor
Safety considerations often tip the scales in favor of pneumatic press packages. Hand stamping inherently places the operators' hands in the striking zone, despite the availability of stamp holders and safety grips. Even with proper safety equipment—like the urethane Safety First stamp grips with 4-inch diameter hand shield—the risk remains present.
Pneumatic presses (combined with a two-hand safety control package) remove the operator from the impact zone entirely. The stamping force is delivered mechanically, eliminating the risks associated with hammer strikes, potential hand injuries, and the repetitive stress that can accumulate over long production runs.
Cost Considerations Beyond Initial Investment
While pneumatic impact press packages require a higher upfront capital investment, the cost analysis should extend far beyond the initial purchase price. Hand stamping's hidden costs accumulate through operator fatigue, potential injury to operator's which could lead to workman's comp claims, quality issues requiring rework, and the training curve for new operators to achieve consistent stamping results.
The "per part" cost equation shifts as volume increases. Hand stamping might cost pennies per part in materials, but when you factor in labor time, potential rework, and the physical limitations of manual processes, pneumatic systems often prove more economical at scale.
Production Volume as the Deciding Factor
The sweet spot for manual hand stamping typically falls below one hundred parts per day for a standard 8-hour shift, especially for simple marking requirements. Beyond this threshold, the efficiency gains from pneumatic systems become increasingly compelling. The crossover point depends on your specific marking requirements—large and/or complex logos or multiple-line text push the balance toward pneumatic systems even at lower volumes.
Consider your growth trajectory as well. If you're currently at 50 parts per day but projecting two hundred within the next year, investing in pneumatic equipment now might save you from a costly transition later.
Making the Right Choice for Your Operation
The decision ultimately hinges on your specific circumstances. Manual hand stamps excel in job shops with diverse, low-volume requirements where flexibility matters more than speed. They're perfect for custom work, prototyping, or operations where marking requirements frequently change.
Pneumatic presses shine in environments with consistent marking needs, higher volumes, or when working with challenging materials. They're the logical choice when operator safety, mark consistency, and production efficiency take precedence over initial cost considerations.
Your material mix also influences the decision. If you're primarily working with mild steel in simple applications, hand stamps might serve you well indefinitely. However, if stainless steel, hardened materials, or complex marking patterns are in your regular mix, pneumatic systems become increasingly attractive.
The key is honestly assessing your current needs while considering future growth. Sometimes the right answer isn't choosing one method over the other—many successful operations maintain both capabilities, using hand stamps for flexibility and pneumatic presses for their higher-volume production runs.
Whatever path you choose, remember that the best marking method is the one that consistently delivers quality results while fitting within your operational constraints. The goal isn't to have the most advanced equipment—it's to have the right equipment for your specific manufacturing environment.