3 min read
A Simpler Marking Solution: The Manual Impact Press
Matt Martin
Tue, May 13, 2025 @ 09:05 AM
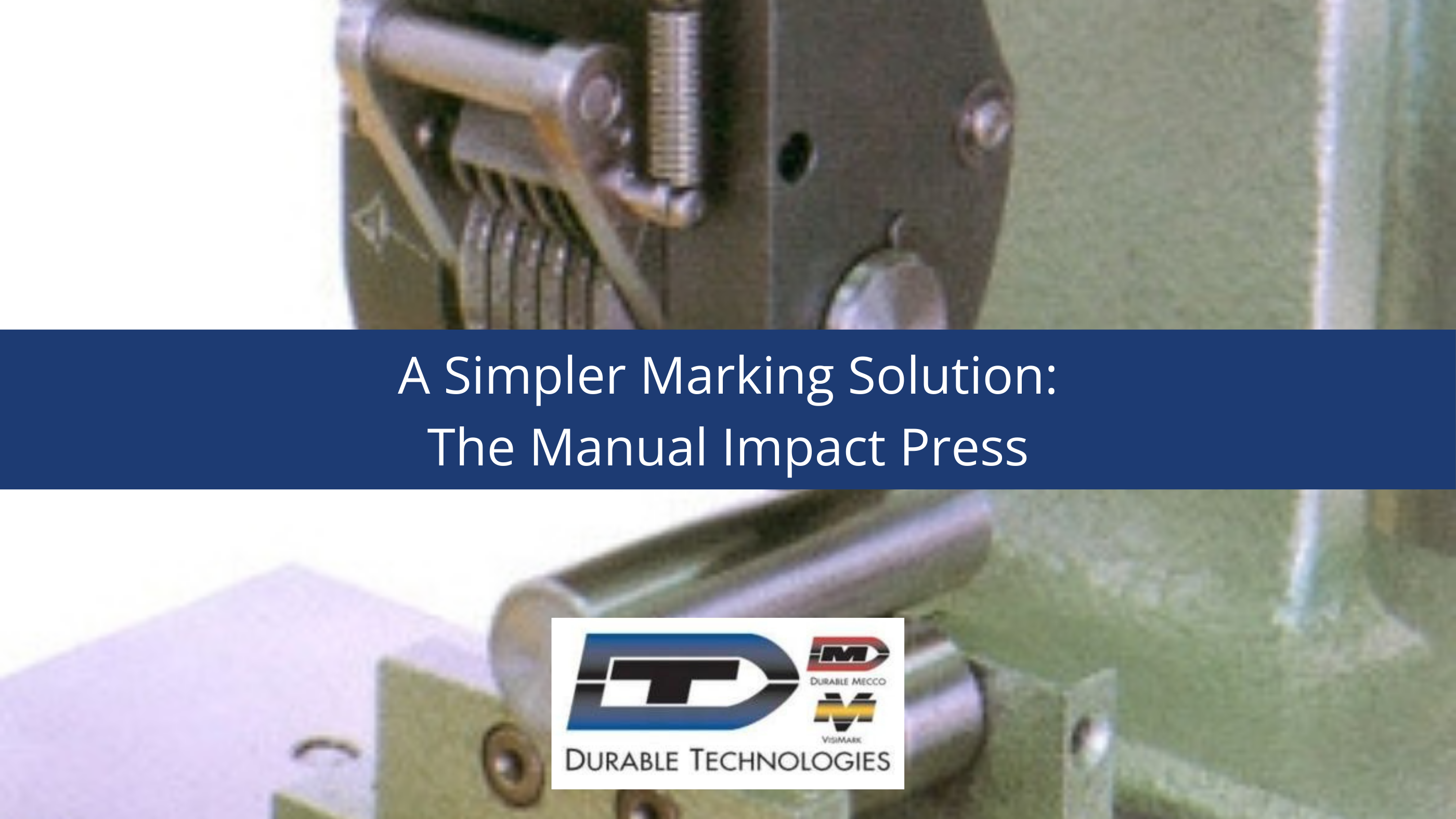
When it comes to industrial part marking solutions, manual impact presses stand out for their reliability, versatility, and cost-effectiveness. Unlike more complicated marking solutions that require extensive maintenance and setup, manual impact presses offer a straightforward approach to creating permanent, high-quality marks on a variety of materials.
Manual Impact Presses and Industrial Marking
The popularity of manual impact presses stems from their unique combination of simplicity and control. These machines provide operators with precise marking capabilities while maintaining an uncomplicated design that reduces downtime and maintenance costs. The manual press delivers consistent results that automated systems sometimes struggle to match, particularly when dealing with varied materials or marking requirements.
For high-volume, repetitive indent marking applications, impact presses achieve remarkably short cycle times that simply cannot be matched by alternative marking methods. This efficiency makes them the preferred choice for manufacturers looking to maintain production speeds without sacrificing marking quality.
The Mechanics Behind Manual Impact Presses
Understanding how manual impact presses work helps appreciate their effectiveness:
Step 1: The energy section advances toward the workpiece through a gear rack and pinion system, powered manually by the operator pulling down the lever.
Step 2: Once the press stroke engages and contacts the workpiece, the process continues with the workpiece held firmly in place by pressure from the energy section—a critical safety feature that prevents movement during marking.
Step 3: As the ball bearings reach their release point, the impact spring discharges its stored energy, delivering a powerful force to the hammer, which strikes the plunger (tool holder). Operators can control the impact force by selecting different springs and adjusting the tension applied.
Versatility: Beyond Simple Marking Applications
What truly sets manual impact presses apart is their remarkable versatility. While they excel at part marking, these machines can handle numerous other industrial applications including:
- Stamping for permanent identification
- Riveting components together
- Staking to secure assemblies
- Forming materials into desired shapes
- Punching precise holes
- Bending metal components
- Crimping wires and connectors
- Piercing materials with accuracy
- Assembling complex parts
- Broaching for internal shaping
- Coining for detailed impressions
This multi-functional capability means that a single manual impact press can serve multiple purposes in a manufacturing environment, maximizing return on investment.
Safety and Reliability in Industrial Settings
Manual impact presses incorporate important safety features that protect operators while ensuring consistent operation. The workpiece holding mechanism prevents movement during the impact process, reducing the risk of misalignment or injury. The mechanical nature of these presses means they're less prone to electronic failures that might affect more complex marking systems.
Their reliability comes from their straightforward design—fewer components mean fewer potential failure points. This translates to extended service life and reduced maintenance requirements compared to electronic or pneumatic marking alternatives.
Choosing the Right Manual Impact Press
When selecting a manual impact press for your operation, consider these key factors:
Force Requirements: Different materials and marking depths require varying levels of impact force. Spring-actuated manual presses from manufacturers like Durable Technologies allow you to select specific springs based on your application needs.
Throat Depth: The distance from the center of the ram to the back of the frame determines what size workpieces you can accommodate.
Stroke Length: This affects how deep your mark can be and how much material can be formed during operation.
Die Compatibility: Ensure the press can accommodate the dies or tools you'll need for your specific marking requirements.
Complementary Marking Components
Manual impact presses work with various marking components to create permanent impressions:
Steel Stamps and Dies: These durable tools come in various character styles, from sharp face for standard metal marking to low-stress options for maintaining part integrity in sensitive applications like aerospace components.
Roll Dies: For applications requiring multiple lines of text or complex logos, roll dies offer an excellent solution that can be integrated with manual impact presses.
Steel Type and Holders: When interchangeable data is required, steel type provides flexibility while maintaining marking quality.
Industries Benefiting from Manual Impact Presses
Manual impact presses serve crucial marking needs across numerous industries:
Metal Fabrication: For permanently marking part numbers, date codes, and manufacturer information on metal components.
Automotive: Component tracking, VIN marking, and quality control applications.
Aerospace: Low-stress marking of critical components where maintaining material integrity is essential.
Oil and Gas: Identification and certification marking that must withstand harsh environmental conditions.
Firearms Manufacturing: Serial number application and proof marking.
Jewelry: Maker's marks and metal purity indications.
The Cost Advantage of Manual Impact Presses
One of the most compelling reasons manufacturers choose manual impact presses is their cost-effectiveness. These machines require minimal initial investment compared to automated marking systems while delivering comparable marking quality. Their mechanical operation eliminates expensive consumables like inks, labels, or etching chemicals that other marking methods require.
Additionally, the low maintenance requirements and exceptional durability mean the total cost of ownership remains manageable throughout the press's extended service life. Small businesses and artisans particularly benefit from this accessibility, gaining professional-grade marking capabilities without prohibitive costs.
Why Manual Impact Presses Remain Industry Favorites
Despite advances in marking technology, manual impact presses continue to be essential tools in industrial marking applications. Their simplicity, reliability, versatility, and cost-effectiveness make them irreplaceable in many manufacturing environments.
Manual impact presses offer the perfect balance of performance and practicality for operations seeking consistent, permanent marking solutions without the complexity and expense of automated systems. Whether marking individual custom pieces or handling high-volume production runs, these presses deliver the quality and efficiency manufacturers demand.
When choosing your next industrial marking solution, consider how a manual impact press might provide the perfect combination of affordability, reliability, and versatility your operation needs.